NIIK offers several main methods of obtaining a commercial grade of urea. These are granulation in a fluid bed, prilling in towers, and granulation in drum granulators. We continue to work on improving the manufacturability and ease of use of all methods.
FLUIDISED BED GRANULATION PROCESS:
NIIK is continuously improving the granulation process. Equipment parts and designs are being improved and tested on the test facility. Further patents are being prepared. We offer our customers our new development - urea granulation plant with the capacity of 3 000 mtpd.
NIIK JSC has patented a unit and method for obtaining granulated product in a fluid bed.
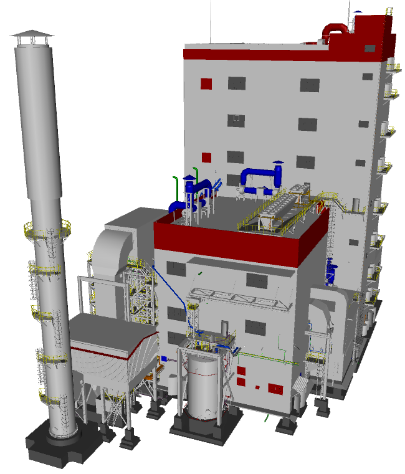
Fluid bed granulation technology is the granulation of urea by spraying a thin layer of liquid urea melt with nozzles onto solid particles of urea seed ("retour") in a fluidised state.
While in the granulation zone, each granule is repeatedly covered with a thin layer of urea melt.
The size increase is uniform for all granules and occurs gradually during the time in the granulation zone, resulting in a uniform shape and high quality of the finished product.
Distinctive features of the fluidi bed granulation unit designed by NIIK are:
- large average size of granules (more than 3 mm)
- high strength of granules of the obtained product (not less than 2.5 kgf/granule)
- high resistance of the product to mechanical influences during transportation and storage
- stable operation of the plant in the range from 60 to 110% of capacity, while maintaining high quality of the finished product
- purification of exhaust air from ammonia and urea dust allows to reduce emissions into the environment up to 20 mg/Nm3 for each substance (with acid recovery). Due to the change of the product movement mode in the nozzle zone, the product removal from the spraying zone is intensified and the influence of changing the air flow rate supplied to the nozzles on the quality of the obtained product is reduced.
Urea prilling process
NIIK has been working on development of urea technology and improvement of urea prilling section since 1960s.
Based on known-how and expertise NIIK developed the following methods of prilling process improvement:
- Increase of urea prills fall height;
- State-of-the art design of a urea priller;
- Installation of an integrated fluid-bed cooler on the prilling tower bottom;
- Advanced scrubbing system for air cleaning from ammonia and urea dust or upgrading of the existing scrubbing system;
- Anti-caking agents by NIIK used for urea prills production.
A modern prilling tower of NIIK design is a structure with a height of up to 100 metres (excluding process pipes) and an inner diameter of the tower shaft from 12 to 21 metres, depending on the required capacity (from 600 to 3000 mtpd and more), simple and reliable in operation.
Advantages of a prilling tower:
- Zero waste: no agglomerates and defected product for recycle and consequently no classifying, crushing and recycle of the defected product: no solid wastes and effluents. For prilling tower having steel and concrete body: equipment and steel structures can be easily disassembled and utilized, resold and relocated.
- High process efficiency: minimal amount of equipment, including dynamic equipment, as the technology has fewer process stages; simplicity and reliability of operation - there is no need for constant washing and maintenance of technological, especially dynamic, equipment, as a result of which no repair and maintenance staff is required.
- Resource saving:
- Lower steam and electricity consumption for process needs compared to a granulation plant;
- multiple less formaldehyde additive in the finished product or no formaldehyde additive at the customer's request;
- no refrigerant supply or additional cooling systems for the finished product are required.
- Cost-effective installation: technology and resource efficiency result in minimal operating, repair and maintenance costs.
- Environmental friendliness: minimal emissions of harmful substances into the atmosphere with the air leaving the tower (ammonia not more than 50 mg/nm3, urea not more than 30 mg/nm3 without acid recovery).
- Product quality:
- resistant to mechanical effects during transport and storage;
- 100% crumbliness;
- monodispersity;
- optimal size and spherical shape of prills, which is very important for dry tucosmixing, uniformity of soil application and farming.
- Capacities range: 600-3000 TPD of the final product.
- Efficiency of investment: CAPEX of a prilling tower construction is lower than CAPEX for a granulation unit.
HIGH SPEED DRUM GRANULATOR UNIT
High speed drum granulator unit (HSDG) is applied for production of granulated fertilizers by dispersing a solution, melt or a suspension on a loose material curtain in a moving air medium in a rotating drum provided with internal blades. The difference of HSDG from other existing drum granulators consists in increase of rotation frequency from 6-12 to 28-35 rpm. This allows to create granules curtain covering the entire cross section of the drum and to intensify the process. Unit filling factor increases from 15% to 75%. Rate of recycling decreases. The finished product is characterized by lower humidity and higher strength.
HSDG unit technical and economic performance
Parameter | Value |
Capacity, t/h | 10 |
Air, м3/t | 1300-2000* |
Water, 3/t | 0-15* |
Electric energy, kWh*/t | 35 |
Moisture removal from 1 m3, kg/h | 30 |
Length, m | 10,6 |
Diameter, m | 2,5 |
HSDG unit technical and economic advantages
- small size: decrease in unit weight and dimensions by process intensification;
- screening and recycling inside the drum granulator;
- easy to install on the existing sites;
- no need in large volumes of air;
- low capital and operation costs;
- wide range of capacity;
- flexibility (depending on the market conditions production of a particular fertilizer type may be quickly launched broadening the range of produced products).
The range of produced products
- straight fertilizers (urea, ammonium nitrate, calcium nitrate, magnesium nitrate, etc.)
- fertilizers with microelements (urea with zinc, copper, iron, boron)
- complex fertilizers with different content of nutrients:
- NS fertilizers (urea with sulphur, urea with ammonium sulphate, ammonium nitrate with ammonium sulphate))
- NP fertilizers (ammonium superphosphate)
- NPK fertilizers (urea+ potassium chloride+ammophos)
- double-layer (ammophos coated with sulphur, phosphogypsum covered with urea, etc.)
The range of complex fertilizers produced by high speed drum granulator unit is very broad. NIIK has not carried out special technical studies aimed at HSDG produced granulated fertilizers diversification. Upon the customer’s request the company may perform experiments in order to explore the possibility of production of a certain fertilizer type by HSDG.
Product quality parameters
Parameter | Value |
Main fraction, mm | 3-5* |
Main fraction content, % wt | min 95 |
Product temperature, 0С oС | 45±5 |
* - may be changed (upon customer’s request).
HSDG unit application
- production of new granulated fertilizers types with enhanced consumer attributes and consequently with a higher demand;
- existing granulation unit capacity increase over design or existing capacity levels which is required for revamps. The primary process of finished product manufacturing is not affected by HSDG unit installation;
- granules fattening – production of 4-5 mm size granules and of the so-called super-granules of up to 8-10 mm size (upon customer’s request);
Services provided by NIIK for prilling towers
- Process monitoring and instructions on prilling process and final product improvement, energy saving, emissions reduction, prilling towers upgrading.
- Feasibility study for a new prilling tower construction and revamp of the existing ones.
- Detail engineering for a new prilling tower construction or revamp of the existing one in any climatic and geodesic conditions.
- Packaged delivery: procurement of materials, control and lock valves, instrumentation, piping; project on turn-key basis.
- Field supervision.
- Technical assistance in commissioning.
- Guarantee performance test.