Technologies for green field and brown field construction of urea plants and revamping concepts
NIIK has been operating in the engineering market in Russia and abroad since 1952. With the direct involvement of the company, the urea industry has been established and is successfully developing in Russia, producing more than 10 million tons of urea annually. The company's portfolio includes documentation on technologies and equipment for urea units of small capacity (500, 600, 700 mtpd), medium capacity (1000, 1200, 1500, 2000, 2600 mtpd), and large capacity (3000 mtpd). NIIK possesses proprietary patented technologies for construction and revamp of urea plants.
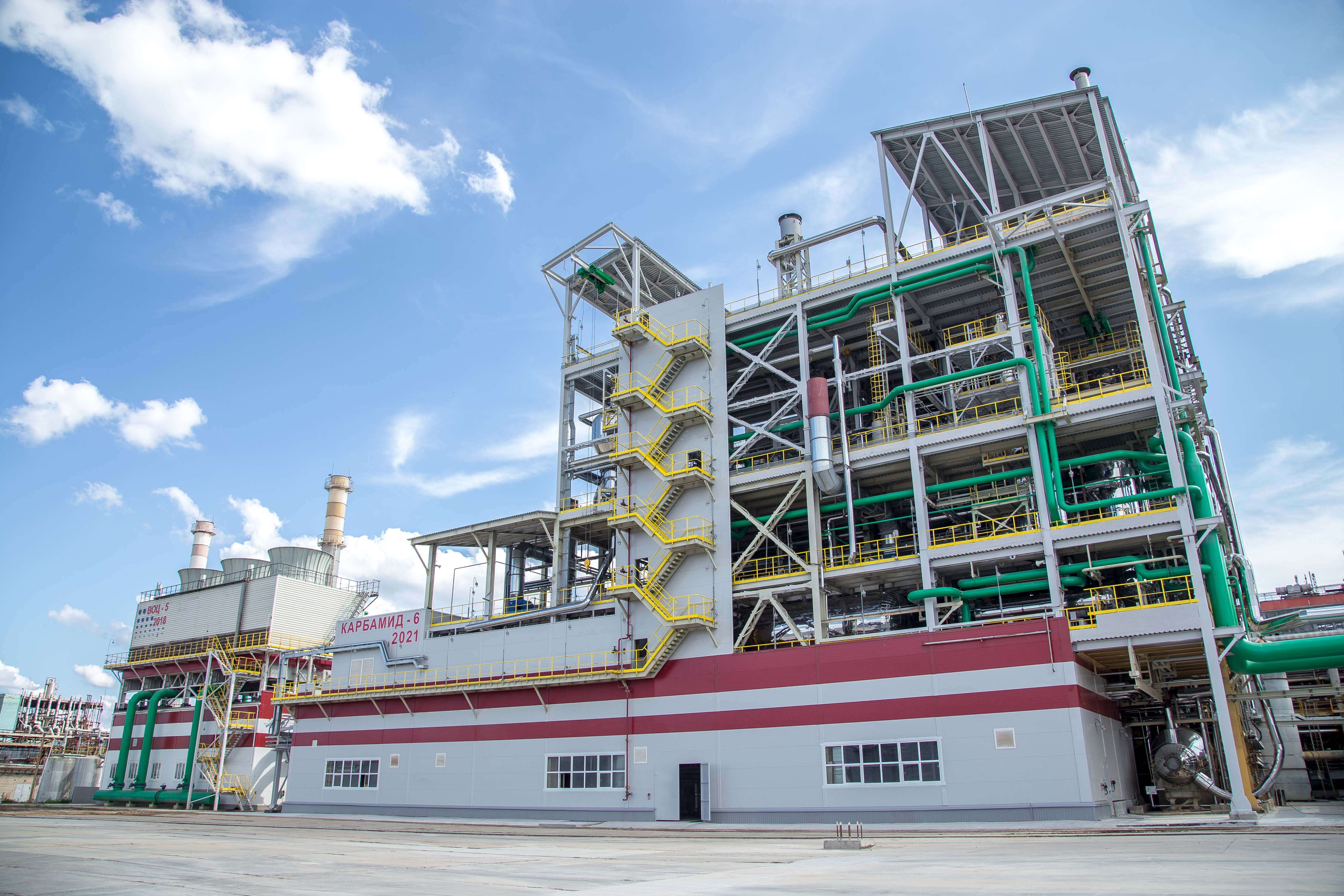
URECON TLR 1000 – is an advanced process of full liquid recycling successfully tested at small scale plants. The technology is based on decades of experience in improving full liquid recycling technology. URECON TLR 1000 uses brand new equipment with optimized hydrodynamics and high efficiency of heat and mass transfer. URECON TLR 1000 process enables the construction and revamp of small-scale plants where small amounts of ammonia need to be converted into urea.
Brief description of the URECON TLR 1000 process:
- Used for smaller production capacities (500 mtpd)
- The design study of a new plant with a capacity of 600 mtpd has been carried out.
- Can be used for the construction of a greenfield plant with a capacity of up to 1,000 mtpd.
- Has advanced technical and economic indicators. Consumption coefficients comprise: for NH3 – 567-570 kg/t, for CO2 – 734-750 kg/t, for steam – 0,8-0,85 Gcal/t.
- Implemented in the course of revamps of functioning shops (a large number of references on plants with full liquid recycling)
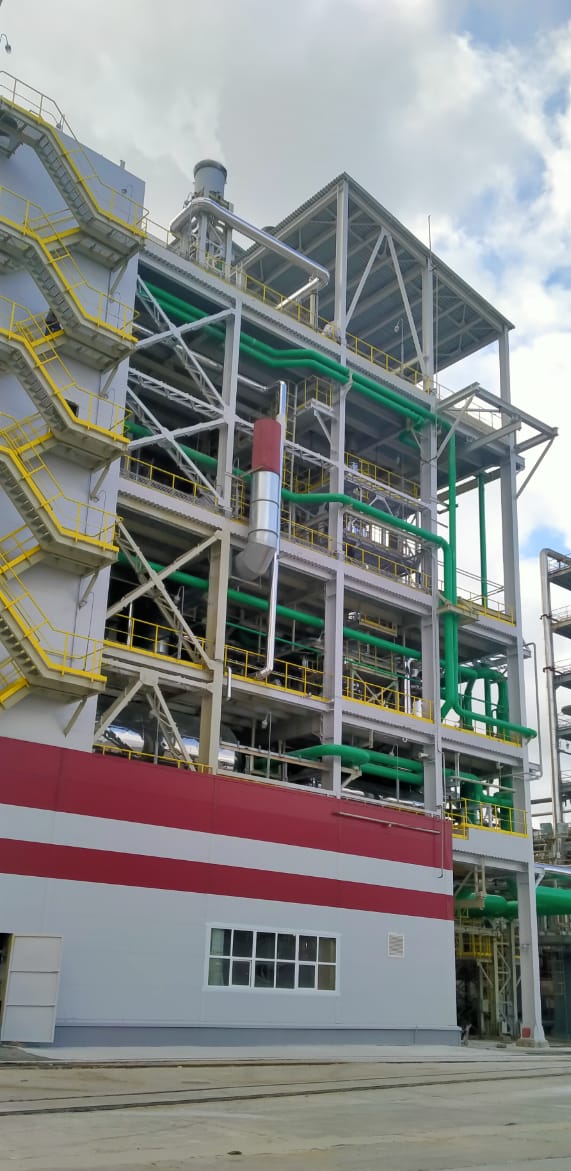
Large-scale URECON process is an advanced stripping process in CO2 current for plants with capacities over 1000 mtpd. The patented design increases the efficiency of the synthesis unit compared to the conventional CO2 stripping process. We consider this process as a technology for greenfield construction of highcapacity units (up to 3000 mtpd). Separate elements of the process can be used for reconstruction of existing stripping production facilities.
Brief description of this process:
- Through more efficient operation of the synthesis unit, the size of the equipment and consequently the investment costs for the construction of the plant are reduced
- The most appealing use of the process is for the construction of new high capacity units
- Technical and economic performance at the international licensor level. Consumption coefficients are: for NH3 – 584 kg/t, for CO2 – 767 kg/t, for steam – 0,756 Gcal/t.
- Potential for revamp of existing units with CO2 stripping process
- Successful commissioning of a 2,050 mtpd unit at PJSC Acron.
- Basic engineering developed for a unit with a capacity of up to 3000 tons per day
- Feasibility study for construction of a 3,150 tpd unit is completed
Main elements of NIIK process:
Set of internal devices to synthesis reactors.
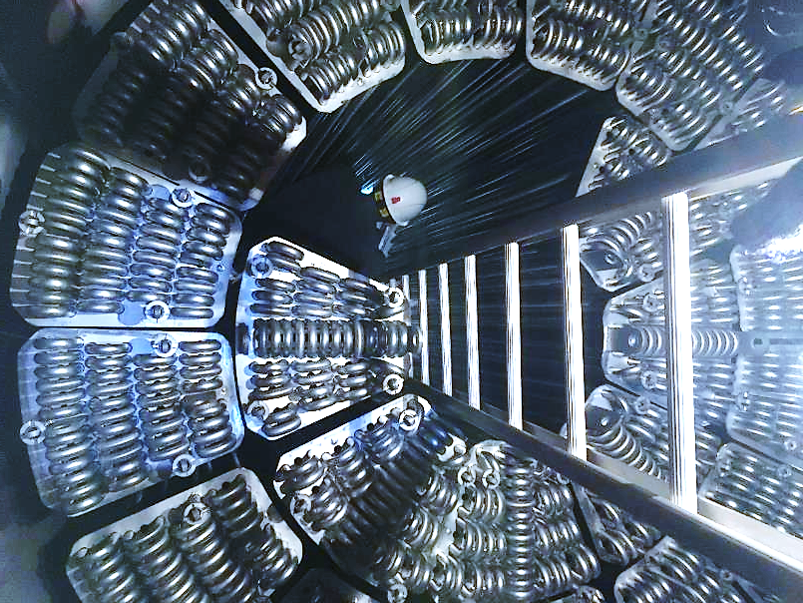
The basis of urea unit is a highly efficient synthesis unit based on a reactor with increased specific productivity, which is achieved by optimizing the hydrodynamics of the flow of raw materials and reaction products in different zones of the reactor in the course of the process. Separation into zones is achieved by installing a set of internal devices inside the reactor. In the first part of the reactor a high-efficiency vortex mixer is installed, which provides mixing of reagents up to the creation of a homogeneous small bubble structure with a developed interfacial surface. In the second part of reactor the conversion booster device creates conditions for binding gaseous feedstock into liquid-phase ammonium carbamate in the hydrodynamic mode of ideal displacement. In the third part, mass-exchange plates are installed to dehydrate ammonium carbamate to form urea and to utilize the rest of the reactor volume. The plates prevent longitudinal mixing of the reaction mixture along the height of the reactor, as well as contribute to additional dispersion of the reaction mixture through the holes in the webs of the plates. In addition to technological advantages, the unit provides reduction of specific energy consumption up to 0.03 Gcal/t.
Distillation units
The main units of the unit, furthermore, include stripping processes at different pressures, carried out in patented film-type units - medium and low pressure distillation units with increased efficiency, heat recovery of ammonium carbamate formation to obtain low pressure water vapor, heat recovery from condensation of medium pressure distillation gases, evaporation units with reduced water vapor consumption.
The final stage of production is obtaining a commercial grade urea.
NIIK offers a wide range of technologies and equipment for obtaining commercial grades of urea.
Prilling - is a process of producing solid prills with a strength of 1000-1300 g/prill from highly concentrated urea melt in prilling towers equipped with an integrated pellet cooling unit and air purification system without exhaust fans. The capacity of prilling towers can be from 1000 to 4500 tons per day. Product temperature should not exceed 500C. Urea dust content in the exhaust air after the cleaning device: not more than 25 mg/m3. Due to the even distribution of melt droplets over the circular cross-section of the tower trunk and organization of the counter uniform air flow, it is possible to significantly increase the density of irrigation of the tower trunk cross-section, and the use of injection system allows to eliminate exhaust fans.
17 prilling towers were built upon NIIK's designs, and 5 towers were revamped. Two more prilling towers are currently under construction. NIIK towers are successfully operated in Russia, Belarus, Ukraine, Uzbekistan, Algeria, Lithuania.
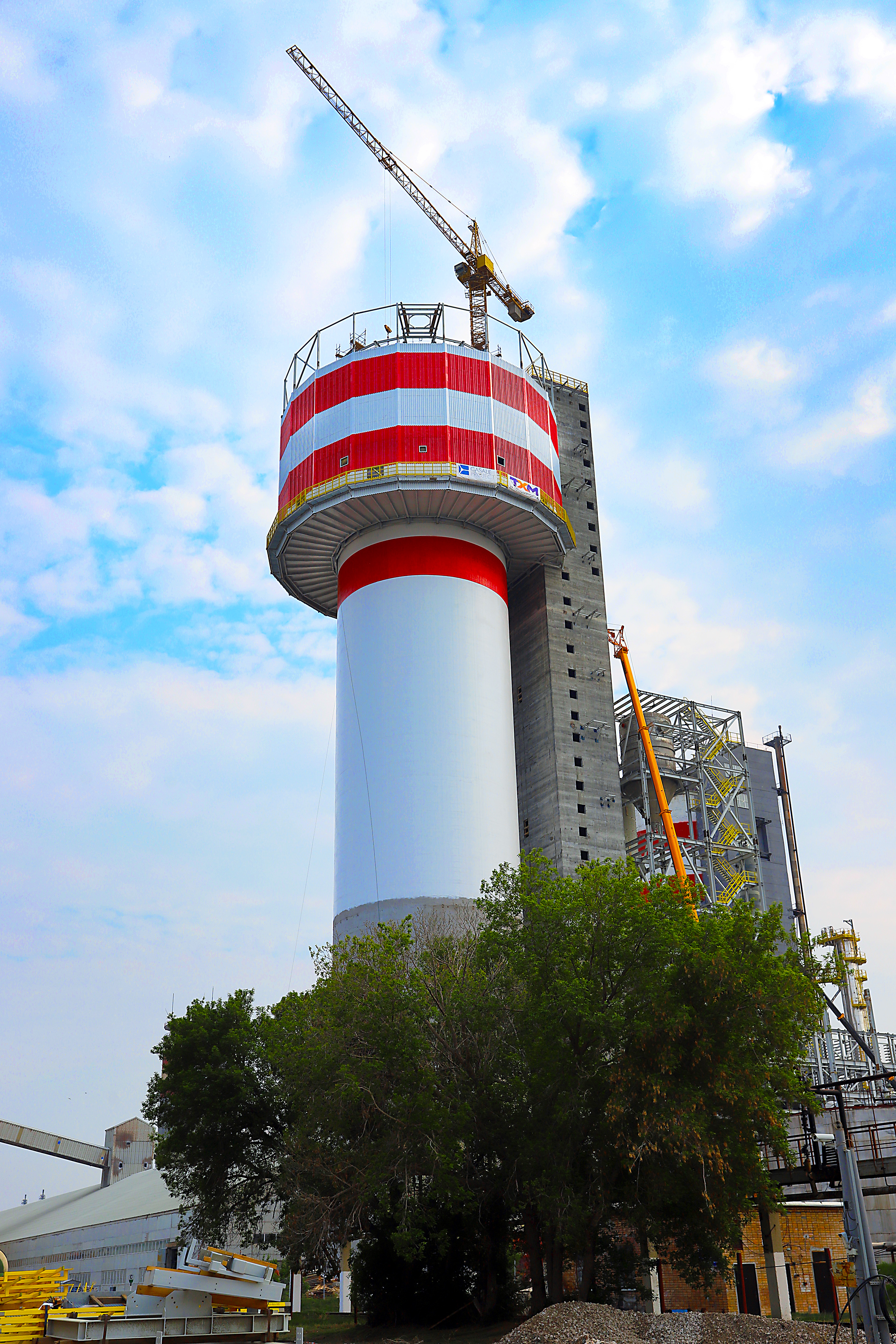
The experience of NIIK stands out not only for the wide list of built and reconstructed prilling towers, but is also unique due to the continuously added operational experience during engineering surveys and dialogue with production facilities. As a result, NIIK can offer the best technical solutions for any customer requirements and support the project all the way to commissioning.
In particular, we have developed technical solutions for the construction of an ammonium nitrate prilling tower with a capacity of 2,700 tons per day.
Granulation - is offered for obtaining solid granules with strength of 2000-3000 g/prill. We offer a national technology of granulation in a fluidized bed with the use of operating nozzles of proprietary design. Compared to prilling, the production costs slightly increase due to additional operations on classification of fine and large pellets, grinding of large pellets and return to the granulator of small pellets as retour.
At the same time, NIIK allows the customer to make his own choice of commercial grade.