- increased quality of process performance
- reduced energy consumption
- improved operational efficiency
- accurate process monitoring & parameters optimization
- improved equipment reliability \extended equipment life,
which is definitely provided by integration of Automated Process Control System into the plant control system.
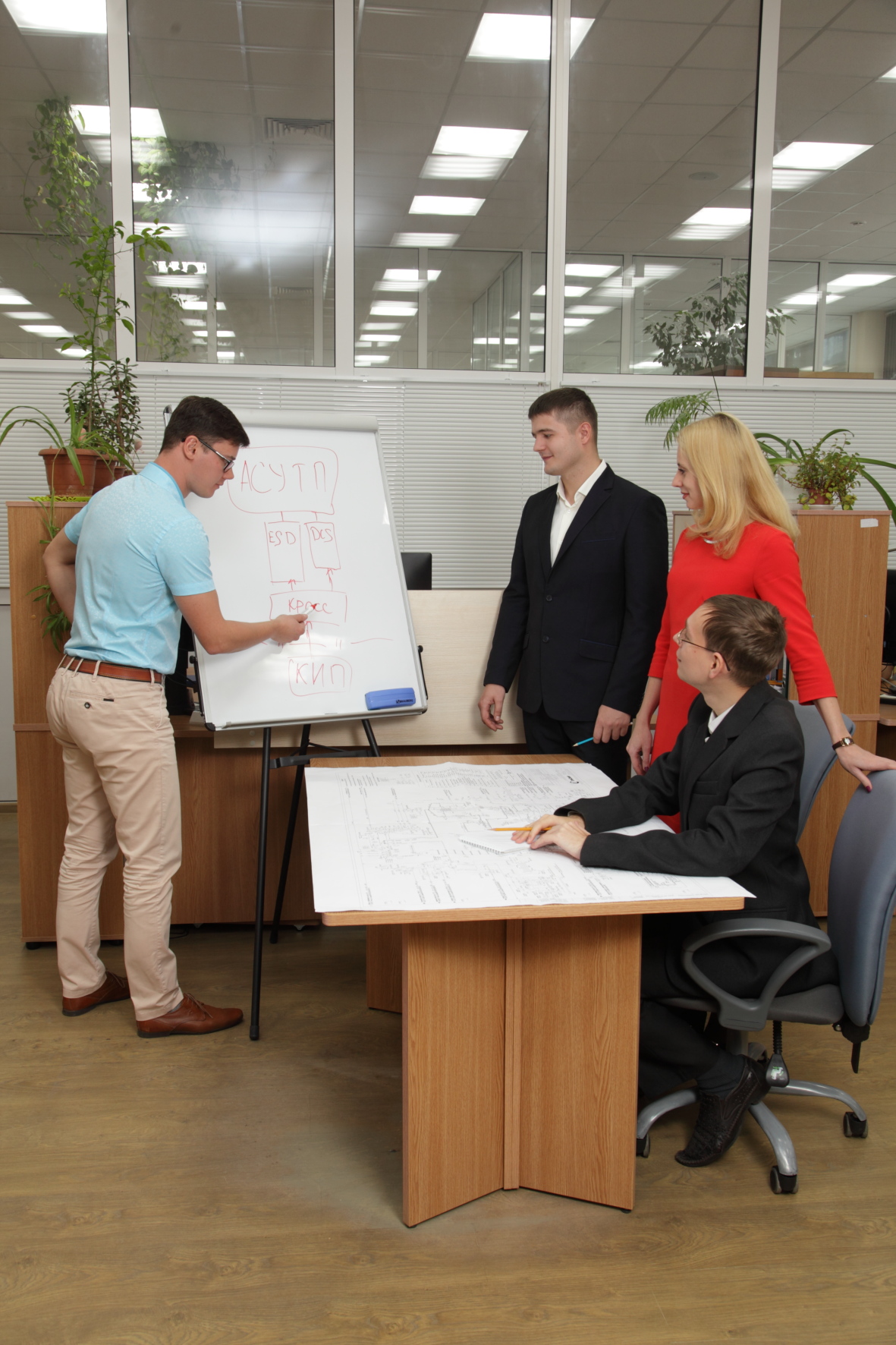
Automated Process Control System designed by NIIK can match your specific equipment or process with the best system for your application reducing your engineering and integration costs, improving productivity, quality and flexibility.
Measurement and testing equipment is provided by recognized and experienced companies working in this field: «Yokogawa», Invensys, Siemеns, АВВ, Emerson, Krohne, Endress+Hauser, Vega, Draeger, Honeywell, JUMO, WIKA.
The fittings of the most trusted brands as Sаmson, Dresser, ARCA are used.
NIIK's offering comprises both basic and detailed design packages for the following sections:
- security alarm system;
- access control system;
- system of video surveillance.
Advanced process control system
- sensors for measuring and transferring information;
- programmable logic controller, realizing algorithms for controlling;
- actuator for operation of final control elements converting signals from logic controller to electrical signals;
- signal generator allowing for monitoring and control;
- technical software and process support of the upper level for remote monitoring, managing and integration with systems of other levels
Optimal Control Systems (OCS)
For economically effective automatic control systems it is necessary to use control algorithms adequate to real objects. Meanwhile the following peculiarities should be taken into consideration: characteristics nonlinearity, multiplicity, nonstationarity, slow response, significant transport and transition delay in control channels, and their complicated operation conditions. Such conditions can be high levels of controlled and uncontrolled disturbances. It should be mentioned that these are not all problematic characteristics of control objects which require relevant solutions within the frame of designed control system structure.
Therefore creation of effective self-supporting APCSs demands a thorough investigation of specific characteristics of processes as control objects; application of up-to-date achievements of process theory, APCS synthesis and analysis methods and of course development of new approaches in this field.
- These problems are successfully solved by the staff of Optimal Control Systems (OCS) department. The department has developed a dynamic optimization system which enables to improve safety and quasioptimal quality of APCS control loops on-line
- Besides there were developed effective control structures (which consider concrete channels specifics and their movements’ conditions) and relevant control algorithms for most essential control loops of urea production process.
- Specialists of the OCS department have invented a new approach how to create a multilevel effective control system of a complicated process object.